APQP (Perencanaan Kualitas Produk Lanjutan)
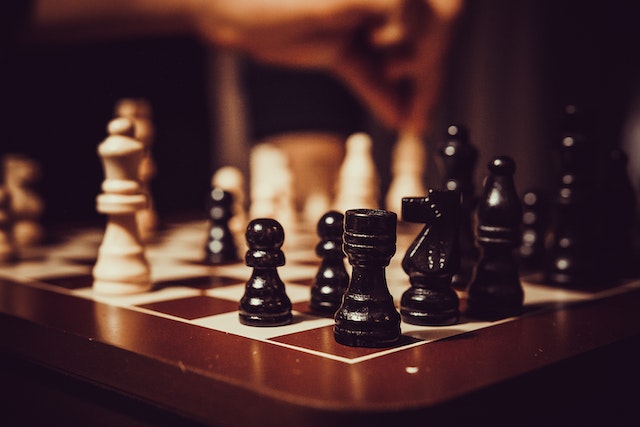
- 1398
- 81
- Miss Wm Hudson
Apa APQP?
APQP (Perencanaan Kualitas Produk Lanjutan), Dalam bahasa Spanyol "Perencanaan Kualitas Produk Lanjutan", adalah kerangka kerja prosedur dan teknik yang digunakan untuk mengembangkan produk dalam industri, terutama dalam otomotif.
Produk dan rantai pasokan yang kompleks memiliki banyak kemungkinan untuk gagal, terutama ketika produk baru diluncurkan. APQP adalah proses terstruktur untuk desain produk dan proses, yang ditujukan untuk menjamin kepuasan pelanggan dengan produk atau proses baru.
Pendekatan ini menggunakan alat dan metode untuk mengurangi risiko yang terkait dengan perubahan dalam produk atau proses baru.
Tujuannya adalah untuk menghasilkan rencana standar untuk persyaratan kualitas produk, yang memungkinkan pemasok desain yang memuaskan pelanggan, memfasilitasi komunikasi dan kolaborasi antara berbagai kegiatan.
Dalam proses APQP, peralatan multifungsi digunakan, yang melibatkan pemasaran, desain produk, pembelian, produksi dan distribusi. Proses ini digunakan oleh General Motors, Ford, Chrysler, dan pemasok mereka, untuk sistem pengembangan produknya.
Fase APQP
APQP berfungsi sebagai panduan dalam proses pengembangan dan juga sebagai cara standar untuk berbagi hasil antara pemasok dan perusahaan otomotif. Itu terdiri dari lima fase:
Fase 1: Perencanaan dan Definisi Program
Ketika permintaan pelanggan memerlukan pengenalan produk baru atau tinjauan yang sudah ada, perencanaan menjadi tema sentral, bahkan sebelum diskusi tentang desain atau desain ulang produk.
Dalam fase ini, perencanaan berupaya memahami kebutuhan pelanggan dan juga harapan produk.
Kegiatan perencanaan termasuk mengumpulkan data yang diperlukan untuk menentukan apa yang diinginkan pelanggan dan kemudian menggunakan informasi ini untuk membahas karakteristik produk.
Dapat melayani Anda: sektor primer: karakteristik, kegiatan ekonomi, kepentinganMaka Anda dapat mendefinisikan program kualitas yang diperlukan untuk membuat produk seperti yang ditentukan. Hasil dari pekerjaan ini mencakup desain produk, keandalan dan tujuan kualitas.
Fase 2: Desain dan Pengembangan Produk
Tujuan dari fase ini adalah untuk menyelesaikan desain produk. Berikut juga evaluasi kelayakan produk. Hasil dari pekerjaan dalam fase ini meliputi:
- Ulasan dan verifikasi desain yang sudah selesai.
- Spesifikasi Bahan dan Persyaratan Peralatan yang Ditentukan.
- Analisis efek dan mode kegagalan desain selesai untuk mengevaluasi probabilitas kesalahan.
- Kontrol Paket Ditentukan untuk Pembuatan Prototipe Produk.
Fase 3: Desain dan pengembangan proses pembuatan produk
Fase ini berfokus pada perencanaan proses pembuatan yang akan menghasilkan produk yang baru atau lebih baik.
Tujuannya adalah untuk merancang dan mengembangkan proses produksi, dengan mempertimbangkan spesifikasi dan kualitas produk, dan biaya produksi.
Proses tersebut harus dapat menghasilkan jumlah yang diperlukan untuk memenuhi permintaan konsumen yang diharapkan, sementara efisiensi dipertahankan. Hasil dalam fase ini meliputi:
- Konfigurasi Aliran Proses Lengkap.
- Efek dan analisis kegagalan dari proses lengkap untuk mengidentifikasi dan mengelola risiko.
- Spesifikasi kualitas dari proses operasi.
- Kemasan produk dan persyaratan finishing.
Fase 4: Proses dan Validasi Produk
Ini adalah fase uji untuk memvalidasi proses pembuatan dan produk akhir. Langkah -langkahnya termasuk:
- Konfirmasi kapasitas dan keandalan proses produksi. Demikian juga, kriteria untuk menerima kualitas produk.
Dapat melayani Anda: Minat Sederhana: Elemen, Cara Menghitung dan Contohnya- Realisasi produksi uji berjalan.
- Tes produk untuk mengkonfirmasi efektivitas pendekatan produksi yang diterapkan.
- Setuju penyesuaian yang diperlukan sebelum melanjutkan ke fase berikutnya.
Fase 5: Peluncuran, Evaluasi, dan Peningkatan Berkelanjutan
Pada fase ini peluncuran produksi skala besar terjadi, menekankan untuk mengevaluasi dan meningkatkan proses.
Di antara pilar -pilar fase ini adalah pengurangan variasi proses, identifikasi masalah, dan awal tindakan korektif untuk mendukung peningkatan berkelanjutan.
Ada juga pengumpulan dan evaluasi umpan balik pelanggan dan data yang terkait dengan efisiensi proses dan perencanaan kualitas. Hasilnya termasuk:
- Proses produksi yang lebih baik, dengan mengurangi variasi proses.
- Peningkatan kualitas dalam pengiriman produk dan layanan pelanggan.
- Peningkatan kepuasan pelanggan.
Contoh
Di mana untuk menggabungkan APQP
- Pengembangan persyaratan dari suara klien, menggunakan implementasi fungsi kualitas.
- Pengembangan rencana kualitas produk yang terintegrasi dalam jadwal proyek.
- Kegiatan Desain Produk yang Mengomunikasikan Karakteristik Khusus atau Kunci untuk Proses Aktivitas Desain, Sebelum Membebaskan Desain. Ini termasuk bentuk dan suku cadang baru, lebih banyak toleransi yang ketat dan bahan baru.
- Pengembangan rencana percobaan.
- Penggunaan tinjauan desain formal untuk memantau kemajuan.
- Perencanaan, Akuisisi, dan Pemasangan Peralatan dan Alat yang Sesuai, sesuai dengan toleransi desain yang diberikan oleh sumber desain produk.
Dapat melayani Anda: Lembaga Ekonomi: Karakteristik, Contoh, Tujuan- Komunikasi saran oleh personel perakitan dan manufaktur tentang cara untuk mengumpulkan produk dengan lebih baik.
- Pembentukan kontrol kualitas yang sesuai untuk karakteristik khusus atau kunci produk atau parameter suatu proses, yang masih berisiko potensi kegagalan.
- Melakukan studi stabilitas dan kapasitas karakteristik khusus untuk memahami variasi saat ini dan dengan demikian memprediksi kinerja masa depan dengan kontrol proses statistik dan kapasitas proses.
Industri yang menggunakannya
Ford Motor Company menerbitkan Manual Perencanaan Kualitas Tingkat Lanjut Pertama untuk Pemasoknya di awal 80 -an. Ini membantu pemasok Ford mengembangkan kontrol yang memadai untuk pencegahan dan deteksi produk baru, sehingga mendukung upaya kualitas perusahaan.
Pada akhir tahun 80 -an, produsen utama industri otomotif di Amerika Serikat menggunakan program APQ. General Motors, Ford dan Chrysler telah diterapkan dan kemudian melihat perlunya bergabung untuk membuat pemasok mereka sebagai inti umum dari prinsip perencanaan kualitas produk.
Pedoman ini didirikan pada awal 90 -an untuk memastikan bahwa protokol APQP berlanjut dengan format standar.
Perwakilan dari tiga produsen otomotif dan American Society for Quality Control menciptakan sekelompok persyaratan kualitas, untuk memiliki pemahaman yang sama tentang isu -isu yang menarik minat dalam industri otomotif.
Metodologi ini sekarang juga digunakan oleh perusahaan progresif untuk menjamin kualitas dan kinerja melalui perencanaan.
Referensi
- Perencanaan Kualitas Produk Lanjutan. Diambil dari solusi NPD.com.
- Perencanaan Kualitas Produk Lanjutan (APQP). Diambil dari kualitas -so.com.