Evolusi pemeliharaan industri dari asal ke saat ini
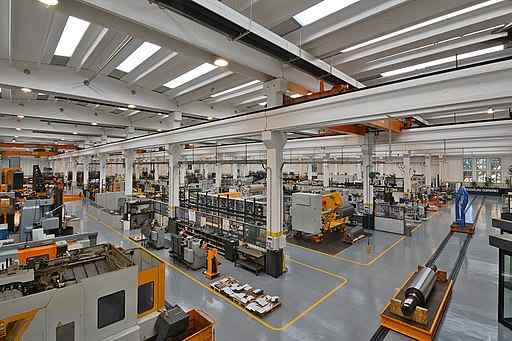
- 4559
- 1293
- Irvin Reichel
Itu Evolusi Pemeliharaan Industri Itu mulai lebih signifikan setelah Perang Dunia Pertama, tahap di mana mesin harus bekerja pada kapasitas maksimum dan tanpa gangguan. Sebelumnya tenaga kerja adalah yang melakukan hampir 90% dari pekerjaan, dibandingkan dengan 10% yang diperkirakan mereka membuat mesin pertama.
Pemeliharaan industri berasal pada saat yang sama bahwa mesin mulai diterapkan untuk produksi barang dan jasa, pada awal abad ke -19. Sebagai karakteristik umum untuk semua fase pengembangannya, kebutuhan untuk membuatnya semakin khusus disajikan.
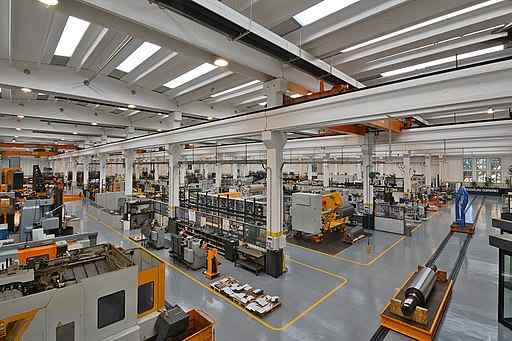
Pemeliharaan Industri adalah bahwa serangkaian langkah -langkah teknis organisasi, yang sebelumnya dapat diuraikan, yang bertujuan untuk mempertahankan fungsionalitas peralatan dan menjamin keadaan mesin yang optimal dari waktu ke waktu.
Di antara tujuan pemeliharaan industri dapat disebutkan: menghemat kapasitas kerja mesin, mengurangi penghentian yang tidak terduga, berkontribusi pada peningkatan produktivitas, menghemat dalam kondisi sempurna alat produksi dengan biaya minimum.
Melalui rencana pemeliharaan industri ini dimaksudkan untuk masa manfaat Anda.
Tugas pemeliharaan industri tidak eksklusif untuk peralatan dan mesin, tetapi dari setiap instalasi tetap atau seluler, layanan industri, komersial atau spesifik, yaitu jenis barang produktif apa pun.
[TOC]
Tahapan dari asalnya hingga saat ini
Generasi Pertama: Dari Revolusi Industri hingga 1950
Itu sesuai dengan Total pemeliharaan korektif, di mana beberapa kerusakan diharapkan untuk dilanjutkan dengan reparasi masing -masing. Fase ini biasanya diidentifikasi sebelum tahun 1950 dan merupakan tahap terpanjang karena dimulai dengan revolusi industri. Biaya pemeliharaan dulu cukup tinggi dan waktu pengangguran untuk menyelesaikan masalah diperpanjang.
Dengan implementasi produksi serial, mengikuti Perang Dunia Pertama, pabrik -pabrik mulai membangun program produksi minimal dan kebutuhan untuk membentuk peralatan yang berkonsentrasi pada pemeliharaan mesin dari jalur produksi dan berkurang ke surat yang mungkin terjadi stop hal berhenti, stop stop stop stop.
Dapat melayani Anda: otomatisasi industriSejajar dengan area produksi maka pemeliharaan yang berfokus pada perbaikan kegagalan korektif atau urgensi. Selain itu, tugas pencegahan ditugaskan untuk menghindari kegagalan.
Pemeliharaan korektif ditandai dengan menghadirkan biaya tenaga kerja yang tinggi dan biaya peluang tinggi, karena ketersediaan cadangan harus segera untuk dapat mengatasi kerusakan yang sedang mendaftar.
Di antara kerugian yang paling jelas adalah pengaruh kualitas karena keausan progresif peralatan, risiko tidak memiliki ketersediaan penggantian yang berarti biaya besar, waktu yang terbunuh oleh kegagalan mendadak dan risiko bahwa masalah lain dapat dihasilkan secara paralel.
Generasi Kedua: Dari 1950 hingga 1970
Pekerjaan pemeliharaan preventif sudah sistematis untuk munculnya Perang Dunia II. Dan beberapa tahun kemudian, American Quality Control Society muncul, yang membantu melaksanakan studi statistik pekerjaan, juga meningkatkan kualitas produk yang diperoleh.
Generasi kedua berfokus pada Pemeliharaan preventif kerusakan, sehingga pekerjaan siklis dan berulang dilakukan dengan frekuensi tertentu untuk pencapaian tujuan tersebut. Fase ini memanjang hingga akhir 70 -an.
Di dalamnya, penggantian pencegahan mulai dibuat, karena hubungan antara waktu seumur hidup peralatan dan kemungkinan kegagalannya ditemukan.
Pemeliharaan preventif memiliki beberapa modalitas: Ini bisa menjadi proses yang harus dilakukan secara berkala, umumnya dengan interval waktu 6 hingga 12 bulan. Itu juga dapat dijadwalkan menurut produsen atau dengan standar yang ditetapkan oleh teknik.
Modalitas lain mungkin bermaksud untuk menerapkan peningkatan dalam proses dan meskipun tidak memiliki frekuensi yang ditetapkan, itu adalah desain ulang untuk mengoptimalkan proses. Akhirnya ada pemeliharaan otonom, dilakukan oleh operator dengan kegiatan sederhana atau rutinitas.
Generasi Ketiga: Dari 1980 hingga 1990
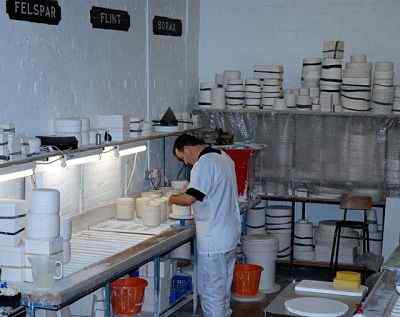
Pemeliharaan diimplementasikan dengan syarat, yaitu, yang tergantung pada pemantauan parameter tergantung pada penggantian atau rekondisi mesin yang akan dilakukan.
Dapat melayani Anda: telegraf: sejarah, penemuan, evolusi, bagaimana cara kerjaPekerjaan ini dimungkinkan berkat ketersediaan peralatan inspeksi dan kontrol yang andal, yang memungkinkan untuk mengetahui keadaan nyata peralatan melalui pengukuran berkala.
Ini adalah waktu Pemeliharaan prediktif, yang terdiri dari deteksi dini dari gejala baru dari masalah di masa depan. Studi penyebab-efek biasanya dilakukan untuk mengetahui asal-usul kegagalan. Elemen yang berbeda pada tahap ini adalah bahwa mereka mulai terlibat dalam area produksi dalam mendeteksi masalah.
Salah satu keuntungan besar dari pemeliharaan prediktif adalah kemungkinan pemantauan dan pendaftaran kegagalan, sehingga akan lebih mudah untuk menjadwalkan perbaikan di masa depan dan lebih sedikit intervensi personel pemeliharaan akan dicatat.
Generasi Keempat: Dari 1990 hingga Hari Ini
Awal fase ini biasanya diidentifikasi pada tahun 90 -an ketika perusahaan AS telah dimasukkan ke dalam dinamika mereka konsep kualitas total yang dipromosikan oleh industri Jepang dari 60. Total Quality Management (TQM) berusaha menciptakan kesadaran kualitas dalam semua proses organisasi dan orang -orang yang mengerjakannya.
Generasi keempat sesuai dengan Total pemeliharaan produktif yang terinspirasi oleh filosofi asal Jepang yang mencari keunggulan atau mengatakan dalam frasa: dapatkan maksimal dengan kualitas yang dapat diterima, setidaknya biaya yang mungkin, dalam pengertian mutiara dan komprehensif. Untuk ini, tugas pemeliharaan kecil seperti penyesuaian, inspeksi, penggantian suku cadang dilakukan, dan interaksi berkelanjutan dengan manajer pemeliharaan.
Program ini berfokus pada faktor manusia dari seluruh perusahaan tempat tugas pemeliharaan preventif ditugaskan untuk memaksimalkan efektivitas barang. Ini mengira tiga prinsip: Selalu menjaga fasilitas dalam kondisi baik, fokus pada peningkatan produktivitas dan melibatkan totalitas staf.
Ini adalah fase sistem perbaikan berkelanjutan dan ditandai dengan implementasi tindakan untuk perbaikan dan pemantauan tindakan. Pemeliharaan menjadi manfaat, bukan kejahatan yang diperlukan, dan diasumsikan sebagai komitmen oleh semua departemen organisasi.
Tujuannya adalah untuk mencapai efektivitas total peralatan yang menyiratkan efisiensi ekonomi melalui ketersediaan, kinerja maksimum dan produk berkualitas.
Itu dapat melayani Anda: sistem mesin manusia: karakteristik dan contohSelain itu, tiga alat lain biasanya diterapkan: rekayasa risiko yang melibatkan penentuan konsekuensi dari kegagalan yang dapat diterima atau tidak; analisis reliabilitas yang mengacu pada mengidentifikasi tugas -tugas pencegahan yang layak dan menguntungkan; Peningkatan pemeliharaan yang terdiri dalam mengurangi waktu dan biaya pemeliharaan.
Pada tahap ini ada perubahan penting dalam undang -undang tentang keselamatan dan kebersihan di tempat kerja, serta praktik yang lebih ramah terhadap lingkungan. Oleh karena itu, perangkat pemurnian, pabrik ekstraksi, pelemahan kebisingan, peralatan deteksi, kontrol dan alarm mulai diterapkan.
Saat ini, para ahli di lapangan memperkirakan bahwa biaya pemeliharaan akan mengalami peningkatan progresif yang akan menyebabkan industri untuk menghasilkan produk pemeliharaan yang lebih andal dan mudah.
Pentingnya pemeliharaan
Pemeliharaan Industri berubah dari menjadi kejahatan yang diperlukan di mana beberapa departemen organisasi berkomitmen dan terlibat. Ini pada dasarnya karena kepentingan sebenarnya dari pengelolaan kegagalan atau masalah peralatan dan fasilitas yang efektif telah diakui, yang dapat memengaruhi salah satu tahap produksi barang atau jasa.
Perlu dicatat bahwa pentingnya pemeliharaan industri terletak pada yang berikut:
- Mencegah kecelakaan kerja dan meningkatkan keamanan untuk orang.
- Mengurangi kerugian karena berhenti produksi.
- Keparahan kegagalan yang tidak dihindari berkurang.
- Mencegah kerusakan yang tidak dapat diperbaiki dalam peralatan atau fasilitas.
- Menjamin kinerja peralatan yang dapat diterima.
- Memungkinkan mendokumentasikan proses pemeliharaan yang diperlukan untuk setiap mesin.
- Memperpanjang masa manfaat peralatan atau barang.
- Mempertahankan barang produktif dalam kondisi operasional yang aman dan sudah ditetapkan sebelumnya.
- Meningkatkan kualitas aktivitas.
- Memungkinkan persiapan anggaran yang tepat, disesuaikan dengan kebutuhan perusahaan.
Referensi
- Muñoz abella, m. (2003) Pemeliharaan Industri. Madrid: Carlos III University of Madrid. Area Teknik Mesin.
- Mora gutiérrez, a. (2009). Pemeliharaan: Perencanaan, Eksekusi dan Kontrol. Meksiko: Editor Alfaomega Grupo.
- Pemeliharaan Industri. (S.F.). Pulih dari ecured.Cu
- Cucu. Riwayat pemeliharaan. (2009, 27 Mei). Diperoleh dari pemeliharaan industri2009.Blogspot
- Villada, “Pemeliharaan sebagai Strategi Kompetitif”, Rev. Fac. Ing. Univ. Antioquia, no. 17, hlm. 7-13, 1998.
- Evolusi Pemeliharaan Industri: Blog: ATS. (2019, 26 Juli). Pulih dari AdvancedTech.com
- « Struktur Sodium Nitrate (Nano3), Properti, Penggunaan, Risiko
- Konsep jarak jauh Euclidian, rumus, perhitungan, contoh »